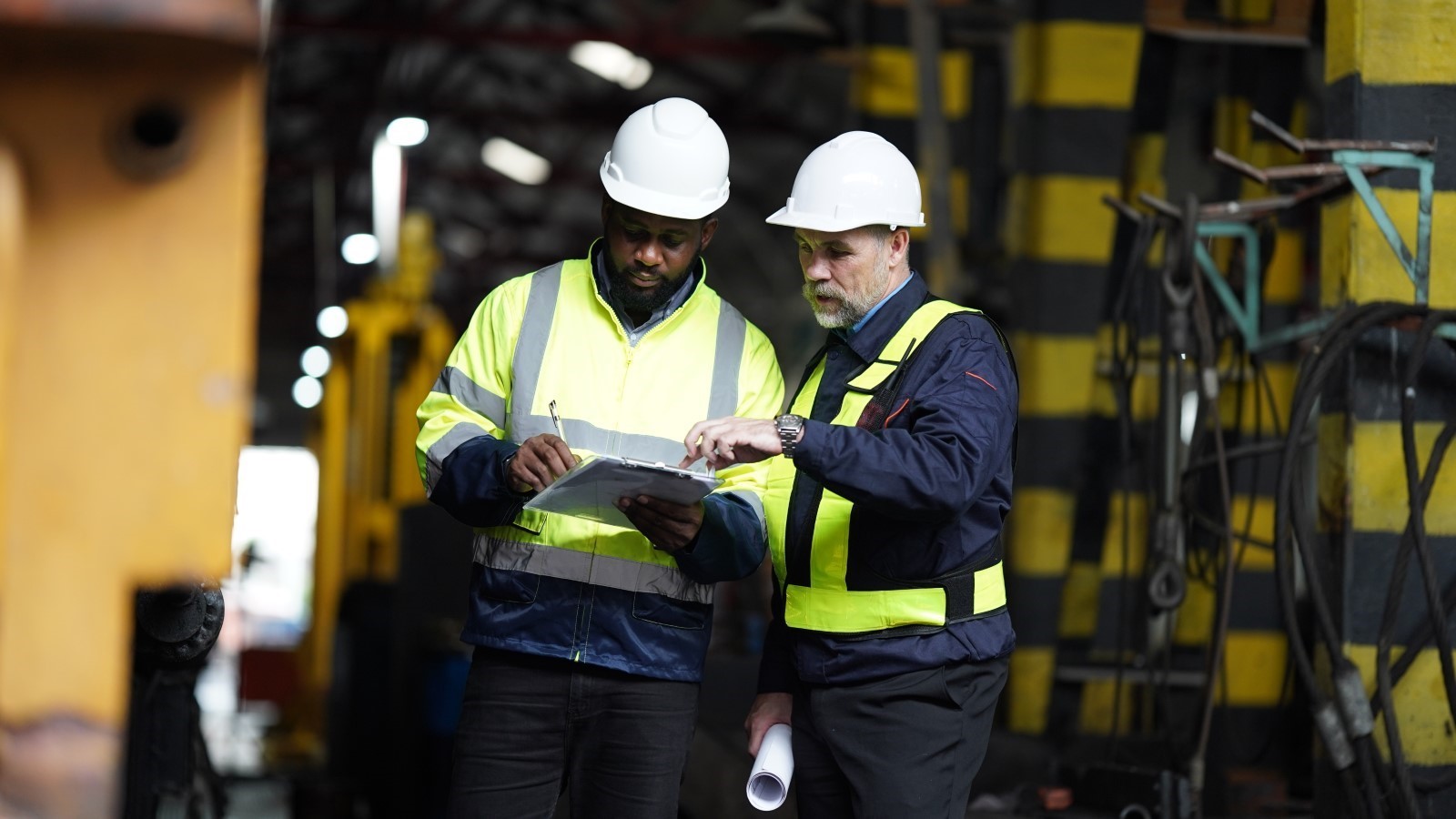
Manutenção em equipamentos de movimentação: quando fazer?
No momento em que compramos um equipamento de movimentação, a última coisa que vamos pensar é sobre a sua manutenção, não é mesmo? Mas saiba que esse processo é tão importante quanto obrigatório para a vida útil do equipamento.
Porém, você sabe quando fazer a manutenção de cada tipo de empilhadeira e paleteira? Então, para saber a resposta desta e outras perguntas, continue lendo este material.
Por que fazer a manutenção para equipamentos de movimentação?
A manutenção preventiva em equipamentos de movimentação oferece uma série de benefícios significativos, que vão desde a redução de custos a longo prazo até a prevenção de acidentes. Portanto, separamos aqui os principais benefícios dessa ação.
Aumento da confiabilidade do equipamento:
Quando as máquinas passam por manutenção, é mais fácil de identificar e corrigir problemas antes que eles se tornem grandes falhas. O que resulta em equipamentos mais confiáveis e operacionais, reduzindo o risco de paradas inesperadas e aumentando a disponibilidade dos equipamentos.
Prolongamento da vida útil:
Ao realizar a manutenção regularmente, componentes desgastados podem ser substituídos ou reparados antes que causem danos irreparáveis, prolongando a vida útil do equipamento, evitando investimentos prematuros em substituição ou, em casos que necessitar, os custos de reparo podem ser menores.
Aumento da eficiência operacional:
Equipamentos bem cuidados tendem a operar com maior eficiência. Assim sendo, o aumento na produtividade aumenta, reduzindo o tempo de inatividade devido a falhas não programadas e melhorando o desempenho geral das operações.
Conformidade com normas e regulamentações:
Um outro benefício da manutenção em equipamentos de movimentação, é garantir que os equipamentos estejam em conformidade com as normas e regulamentações de segurança, sobretudo para evitar penalidades legais e manter um ambiente de trabalho seguro.
Prevenção de acidentes:
Veículos em suas condições normais são menos propensos a falhas inesperadas que poderiam resultar em acidentes. A manutenção preventiva reduz os riscos de situações perigosas, gerando segurança para os operadores e outras pessoas envolvidas.
Melhoria da qualidade do trabalho:
As máquinas que passam por manutenção preventiva regular funcionam de maneira mais consistente, o que contribui para a qualidade do trabalho. Isso é especialmente crucial em operações onde a precisão e a confiabilidade dos equipamentos são essenciais.
Programação de manutenção planejada:
Por fim, a manutenção permite que as atividades de inspeção sejam programadas em momentos convenientes, evitando interrupções significativas nas operações normais.
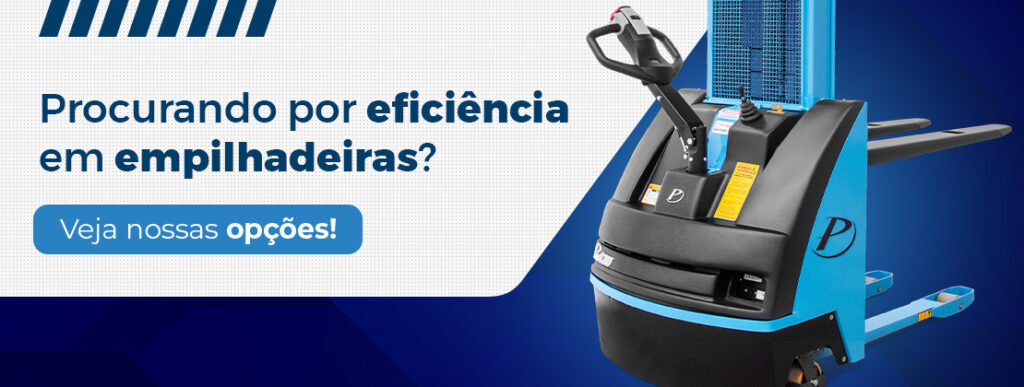
Calendário de manutenção
Ao pensar na durabilidade e eficiência dos equipamentos de movimentação, a implementação de um calendário de manutenção estruturado é fundamental. Então, dividindo as atividades em categorias de frequência, podemos garantir uma abordagem abrangente e eficaz. Confira!
1. Manutenção diária:
- Verificar sinais de desgaste, vazamentos e danos externos;
- Aplicar lubrificantes conforme as especificações do fabricante;
- Garantir o funcionamento adequado dos controles e sistemas.
2. Manutenção semanal:
- Avaliar a eficiência do sistema de freios;
- Certificar-se de que correntes e cabos estão tensionados corretamente;
- Remover sujeira e detritos para prevenir danos.
3. Manutenção mensal:
- Avaliar níveis de óleo e fluido hidráulico;
- Assegurar que os sensores estejam calibrados corretamente;
- Verificar a pressão e condição dos pneus.
4. Manutenção trimestral:
- Avaliar a capacidade de carga do equipamento;
- Verificar soldas e componentes estruturais;
- Substituir filtros de ar, óleo e combustível.
5. Manutenção anual:
- Realizar uma inspeção abrangente de todos os componentes;
- Trocar peças que atingiram o limite de desgaste;
- Executar testes de segurança e sistemas de emergência.
Ressaltamos que, apesar de fornecemos um calendário geral, é necessário que você analise as necessidades e condições específicas do seu ambiente de trabalho. Sinta-se à vontade para fazer substituições e adaptações que julgar necessárias.
Contudo, a fim de facilitar para você, criamos um Service Book que inclui um Plano de Revisão. Ele contempla instruções para diversos modelos de veículos industriais. Clique no botão abaixo e garanta esse material gratuitamente.
Sinais de alerta e inspeções visuais
Sinais de alerta comuns:
Sabemos da responsabilidade que se deve ter ao operar esses tipos de máquinas pesadas, é crucial estar atento a sinais de alerta que podem indicar a necessidade iminente de manutenção. Identificar esses sinais precocemente pode evitar falhas significativas e reduzir custos. Alguns sinais de alerta comuns incluem:
- Ruídos anormais: barulhos incomuns durante a operação podem indicar desgaste em peças internas ou problemas nos componentes.
- Vazamentos de fluidos: observar vazamentos de óleo ou fluido hidráulico pode indicar problemas nos sistemas e requer intervenção imediata.
- Variações de temperatura: aumentos repentinos de temperatura podem sugerir problemas no sistema de resfriamento, exigindo uma inspeção mais detalhada.
- Vibrações excessivas: vibrações fora do comum podem ser indicativos de desalinhamento, peças soltas ou problemas nos rolamentos.
- Desempenho diminuído: se o equipamento apresentar uma redução perceptível no desempenho, isso pode apontar para desgaste ou falhas nos componentes.
Inspeções visuais regulares:
As inspeções visuais regulares são uma linha de defesa essencial para identificar problemas precocemente e garantir a segurança e eficiência dos equipamentos, sendo as principais:
- Verificação de fluidos: inspecionar regularmente os níveis de óleo e fluido hidráulico, identificando qualquer sinal de vazamento.
- Análise de desgaste: observar o desgaste em peças, como correias, correntes e engrenagens. Afinal, isso pode ajudar a prever quando é necessário substituí-las.
- Limpeza e remoção de obstruções: manter os componentes limpos e livre de detritos é essencial, pois obstruções podem causar danos e afetar o desempenho.
- Teste de controles e sistemas: realizar verificações visuais nos controles e sistemas para garantir que estejam funcionando corretamente.
- Inspeção estrutural: verificar soldas, parafusos e outros componentes estruturais para identificar qualquer sinal de desgaste ou danos.
Agora você já sabe que a manutenção preventiva não é apenas uma prática corretiva, mas sim uma abordagem proativa para preservar a integridade dos equipamentos. Já que, ao identificar e corrigir problemas antes que se transformem em falhas sérias, esta estratégia contribui para a redução de custos a longo prazo, aumento da confiabilidade operacional e prolongamento da vida útil dos equipamentos.
Considerar a consultoria especializada pode ser valioso, trazendo conhecimento técnico e insights personalizados para otimizar os procedimentos de manutenção. É ainda melhor contar com uma equipe especializada para realizar os procedimentos necessários e para isso que estamos aqui!
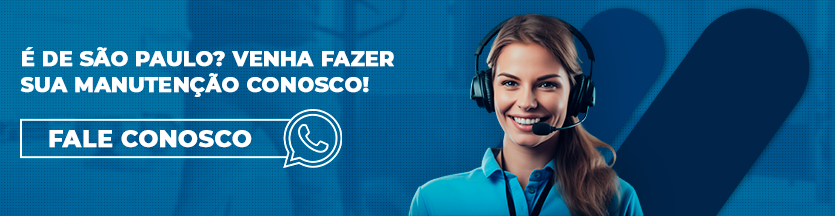
E caso não seja de São Paulo, procure por outras empresas capacitadas e de sua confiança.
Esperemos que tenha gostado do conteúdo e te recomendamos, ainda, que leia: Planejamento 2024: como organizar a logística no ano novo